5 Tips to Optimize Your Metal Spinning Design
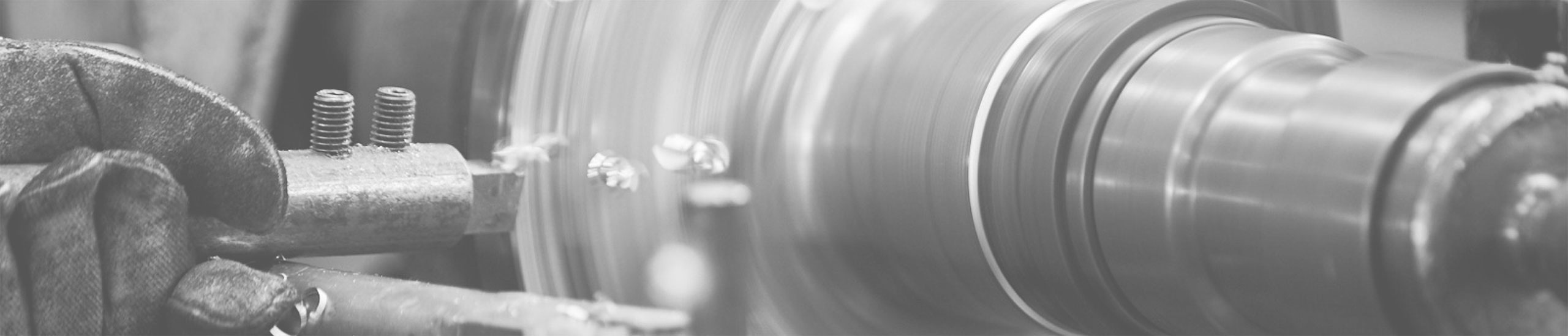
Metal spinning is an advantage when you need seamless items or particularly strong structural parts. The process is ideal for production volumes ranging from short-lead prototypes to mass production.
Nearly any type of metal can be used for metal spinning, including brass, copper, aluminum, carbon steel, stainless steel, or titanium.
Best results may be achieved by carefully following the best practices for metal spinning planning and design.
1. Define Object Function If you don’t know exactly what you’re designing, you’re more likely to waste time and materials during the spinning process. It’s important to note that metal can only be spun on both circular or semi-circular shapes, so the process can, in fact, work for designs that require sharp corners.
Once the final goal is determined, a design can be created that will leverage metal spinning’s precision and customizability.
2. Pick Your Material Metal spinning works with a variety of metals, but selecting the appropriate materials for your specific job will ensure the best results and minimize wasted metal. Different metals can have vastly different end results, depending on the thickness you wish to achieve.
Very small changes in diameter or thickness can make a part unusable for your engineering project. In addition, some metals are more likely to get rigid as they are spun.
3. Consider Material Thickness Depending on the type of metal you use and the height of the sidewalls, the sidewalls of your object will thin and could vary as much as 25%. You’ll need to carefully consider the amount of pressure you apply from the mandrel to the raw metal.
A larger corner radius will be easier to create and stronger than using tighter corners, so you’ll want to avoid sharp corners in your finished part.
4. Specify Your Tolerances Metal spun parts don’t necessarily need consistent thickness throughout. Designs should also note that part diameter can be impacted by roundness and flatness.
In parts that are less than 1 foot in diameter, a tolerance of +/- 0.005 inches may be achieved.
5. Cost Factors Many metal forming methods are not cost effective at low volumes, but you can save time and money by metal spinning prototypes or a short runs. A cost/benefit analysis can help you identify savings for your unique design.
Creating parts is fast with metal spinning so lead times may be shorter, but it’s important to create a design that facilitates fast and accurate production.
Metal Craft Spinning and Stamping is a fourth-generation, family-owned business that specializes in the production of high-quality parts for our customers across the United States and North America. If you’re ready to bring your metal spinning design to life, please request a quote to get started.